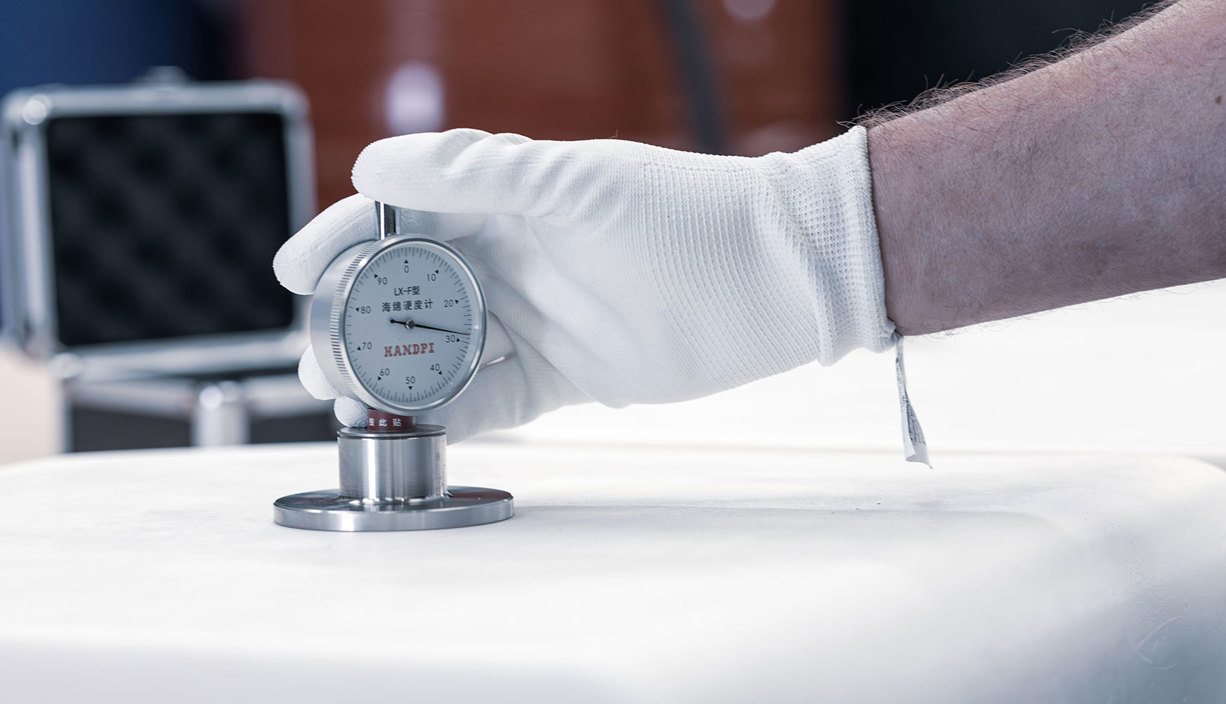
The aviation seat cushion industry has seen limited bio-based innovation — until now. Muirhead's BioPRO® Foam introduces a groundbreaking approach to sustainable comfort by harnessing protein-based technology in an unprecedented way.
As a proprietary and patented innovation, BioPRO® establishes a new product category, offering a fresh alternative to conventional foams. With its unique composition, technical performance and environmental sustainability, it represents a significant step forward, poised to revolutionise the seat foam market. The moulded cushions made from BioPRO® ensure consistent shape and size, guaranteeing a uniform appearance throughout the cabin.
Made with 20% protein content – which replaces the problematic substances and forever chemicals found in traditional seat foam – BioPRO® is more natural and sustainable by design. It has remarkable durability and is naturally fire-resistant outperforming traditional foam products on both metrics.
Our foam is custom-moulded to your exact specifications regarding shape, weight, density, and more. As it is moulded rather than cut, this process generates zero waste during production.
From by-product to protein-based innovation
Muirhead has, for a number of years, been looking to find alternative uses for hydrolysed collagen, which is a by-product of our leather-manufacturing process.
During our initial exploration, we noticed that this hydrolysed material could foam and gel and it was also fire-resistant. This sparked an idea and presented us with a challenge — could we use this collagen to create a superior seat cushion for the aviation industry?
Not all bio-content is created equal. Many manufacturers claim high bio-content, yet, much of it comes from plant-based polyols that rely on plastic bonding agents. Often, these additives don’t integrate into the foam structure, leading to premature breakdown, reduced durability, and compromised performance.
BioPRO® takes a different approach. By chemically bonding 20% natural biomass — specifically hydrolysed collagen sourced from our own manufacturing process —our bio-content becomes an active, functioning part of the foam.
As the third most prevalent natural material on Earth, collagen possesses unique properties that make it an ideal component: it foams, gels, and resists fire under extreme conditions. The result? A high-performance, environmentally sustainable seat cushion alternative that replaces fossil fuel-derived components while significantly reducing carbon emissions in aircraft interiors.
Muirhead already has a stellar reputation for supplying high-performance leather for seating – so the next obvious application was to put our leather on a biofoam cushion that is made from our own collagen. It’s an innovation that fits seamlessly into our vertically integrated, circular approach.
After five years of painstaking research, development, chemistry, analysis, rigorous testing and prototyping – we are proud to present a finished bioprotein product —one that is set to reshape expectations in the aviation seat foam market.
The only foam that’s naturally fire-resistant
Traditional seat foam is extremely flammable, which isn’t practical for a highly regulated industry like aviation. To overcome this, other manufacturers will add permanent chemicals, melamine, and other halogenated flame retardants to their products to ensure they are fire-resistant enough to fly.
BioPRO® is 100% free of such substances. Instead, we chemically bond hydrolysed collagen to conventional foam chemistry, creating a stronger set of bonds that provide greater comfort, durability, and an intumescent end result — it is naturally fire resistant. When you apply a flame, BioPRO® simply chars on the surface. Having conducted external tests, our C-burn performance data shows full compliance with international standards.
“The key aspect is that the tertiary amine groups of the hydrolysed protein are bonded to the other ingredients, forming stable bonds and producing a more functional material.” Dr Warren Bowden, Head of Innovation and Sustainability
The addition of forever chemicals and other substances is also extremely detrimental to every other aspect of the foam’s performance. Whereas, the hydrolysed collagen we use actually improves the performance of our foam, in a number of ways.
Superior durability as standard
The first example is durability. The fillers that other manufacturers use are simply suspended within their foam, which causes internal abrasion every time the foam is compressed and only serves to break it down over time. Essentially, the product destroys itself from within and relatively quickly.
However, if all of the material, including the protein which is bound, acts as a foam – and nothing is in suspension – then that degradation doesn’t occur to anywhere near the same extent. This is a huge benefit of BioPRO®
Because our bio-content is chemically bonded, it becomes a functioning part of the foam, resulting in no internal abrasion whatsoever. This ensures that our product performs better across every measurable test – it is more durable, more reliable, more comfortable and longer-lasting.
“With our own indicative testing we can make the very best foam that’s fit for purpose – not just a product that passes one test at the expense of other performance metrics.” Scott Hadley, Foam Technology Expert
Lightweight innovation without compromise
Moulded foams were historically overlooked in aviation because they were too heavy — despite offering superior durability and comfort. But BioPRO® changes that equation.
Our advanced manufacturing process achieves significant weight reductions while maintaining — or exceeding — performance expectations.
At 47kg, BioPRO® delivers exceptional durability and precision, supported by repeatable test data and strict manufacturing tolerances. Unlike conventional lightweight foams, which often suffer from inconsistencies and shorter lifespans, BioPRO® offers unmatched reliability. It meets or exceeds OEM and airworthiness standards, proving that lighter weight doesn’t mean sacrificing strength, longevity, or safety.
Tailored comfort for every passenger
Comfort isn’t one-size-fits-all, especially in aviation seating. That’s why BioPRO® is designed to adapt, providing targeted support for different body types. Independent testing has shown its ability to deliver exceptional ergonomic performance, ensuring a superior seating experience for a wide range of passengers.
But we go further. Our foam chemistry is fully adjustable, allowing us to fine-tune formulations to meet specific comfort needs — whether it’s enhanced support, softness, or durability.
“At AIX, we are introducing three core BioPRO® products—lightweight, standard, and high density—each available in soft, medium, and firm comfort levels. That’s nine tailored solutions, all backed by extensive durability data, providing aviation designers with a high-performance alternative that balances lightweight engineering, comfort, and safety." Scott Hadley, Foam Technology Expert
Sustainable every step of the way
The elimination of concerning substances such as melamine, bromine and PFAS (forever chemicals) and the inclusion of 20% bio-content within our foam bring clear environmental benefits. Added to that, the fact that our foam is longer-lasting will naturally reduce the need for replacements – but there are also huge advantages to BioPRO® when that time does come.
There are production benefits, too. Traditional foam is typically cut to the desired shape and size from gigantic, externally sourced blocks of foam, meaning that the surplus and the wastage are colossal. With BioPRO®, however, we size and shape our products by creating and filling bespoke moulds for every client and every order, ensuring better precision and absolutely zero waste.
“First we look at the end shape. We design moulds in-house and gather info to create our base chemistry. We blend the chemicals in various ways, then inject the mix into the mould under pressure and heat. It’s actually a simple process, all the work is in the front-end chemical recipe.” Scott Hadley, Foam Technology Expert
The benefits of complete control
Beyond size and shape, the bespoke nature of our foam allows it to be tailored precisely to your specifications, including weight and density. This level of customisation gives you greater control over the final product, helping you achieve the ideal balance between performance and passenger comfort.
As the base material manufacturer, we oversee the entire production process — from farm to fit. Our single-source approach eliminates the need for external suppliers, streamlining operations, reducing overheads, and ensuring seamless communication through one point of contact. This also provides access to Muirhead’s specialised design and testing teams, ensuring a fully customised, high-performance end result.
By meticulously crafting our natural aviation leather, BioPRO® Foam, and seat covers in-house, we deliver a fully integrated seating solution with precision, consistency, and superior aesthetics. Unlike traditional cut foams, our moulded cushions retain their exact shape and size, ensuring uniformity across the cabin while enhancing visual appeal and passenger comfort. This seamless integration not only simplifies logistics but also enhances operational efficiency.
Partnering with Muirhead streamlines the development process, reduces lead times, and simplifies the supply chain through a single point of contact. This efficiency translates to cost savings and a more straightforward project management experience.
Additionally, our pre-fitted seat covers and cushions cut assembly time, further optimising operational efficiency. This comprehensive solution elevates the passenger experience while providing airlines with a reliable, efficient, and aesthetically refined seating option.
Muirhead: a history of innovation
Muirhead’s success is built on 185 years of continuous innovation. Whether it’s new opportunities for circular manufacturing, new products and services, or new uses and re-uses for our by-products, we have never stopped exploring new ideas and inventing new ways to do business.
Our proprietary BioPRO® Foam is just the latest in a long line of Muirhead innovations. But, given its numerous advantages, its natural sustainability and its potential to completely revolutionise an entire industry, it’s one we are extremely excited about.
To find out more about Muirhead BioPRO® Foam, and to test it out for yourself, pay us a visit at the Aircraft Interiors Expo 2025 (AIX), Booth 6E95.