A better, simpler seat cover service.
As the world’s most trusted supplier of leather for aviation and rail travel, we know a thing or two about passenger seating. And we know even more about the intricacies and challenges of using leather as your base material for creating high-quality seat covers.
Across the globe, most seat cover cut-and-sew facilities are geared up for manufacturing with fabric and synthetic materials, which account for around 80% of the market. But such processes aren’t suited to leather, and can lead to issues with production and performance, as well as increased costs and timings.
Introducing… the Muirhead Seat Cover Service.
The new Muirhead Seat Cover Service aims to simplify, streamline and enhance every aspect of the process. This is a strategic expansion that aims to disrupt traditional seating supply chains with a unique, vertically integrated service model.
Our end-to-end approach takes customers all the way through research, design, testing and production to fully finished, high performance, leather seat covers. These will be operational, in the air, for 10 to 12 years, and they come with a 7-year warranty. In stark contrast, alternative fabric and synthetic materials have a much shorter lifespan of only 3 to 4 years.
And the benefits don’t end there…
Leather expertise where it matters most.
High-performance leather isn’t just the luxury choice, it’s the smart choice – more efficient, more hygienic, more environmentally sustainable, harder-wearing and longer-lasting. Which is why it’s the first choice for many travel operators. But, as a manufacturing material, leather is unique; it functions differently.
“Leather is a natural product that requires specific techniques, engineering science, and dedicated knowledge and expertise. Which is exactly what we offer.” - Martin Longden, Head of Cabin Engineering
Muirhead has been supplying aviation leather to traditional cut-and-sew facilities for decades and the issues they have are almost always the same. Problems arise because of how these facilities use the leather, laminate it, pattern it, cut it or sew it. And, in some cases, because it’s actually the wrong type of leather that has been specified.
These are the problems that we are called in to diagnose and fix. Which we do, because we understand leather. We know how to engineer it, how to manipulate it, how to manufacture with it and how best to process it, from farm to fit. To put it pointedly, we take the hassle out of leather.
“We can see straight away when fabric processes have been used for leather. So, for us, it’s always an easy fix.” - Charlotte Clayton, Cabin Engineering Manager
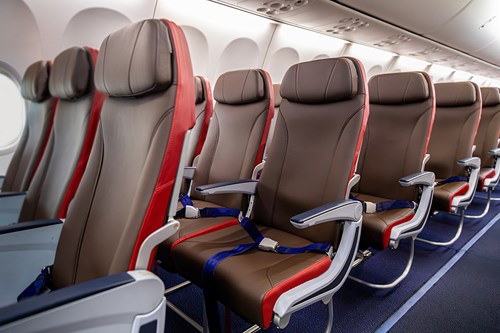
One supplier. Many benefits. Zero headaches.
A big advantage of the Muirhead Seat Cover Service is that you work with one trusted supplier, removing any and all complexity from your supply chain.
Control: We own the whole process, from tanning to sewing, which means you have a single point of contact throughout. This reduces handling, it reduces risk, and it reduces supplier disputes, because we can offer full accountability and ensure traceability of the entire process.
Speed: As a leather manufacturer, we have the capacity to cut through your current lead times. As soon as our leather is made, it’s ready to use, can be sent direct, and turned round in a week or less. No shipping back and forth, no 12-week wait. Even for replacement parts, we keep a stock handy to ensure the fastest possible service.
Sustainability: Our end-to-end service reduces production waste, naturally, as we only ever make and use what we need. Our superior knowledge of leather also reduces the number of issues that occur and replacements that are required, again reducing waste. And our faster service means that our supply chain is set up to use rail rather than air, limiting our environmental impact as much as possible.
Cost Savings: There are huge cost efficiencies too, as we can reduce your margin stack by removing the need for separate cut-and-sew facilities and any other middlemen. We are your one-stop shop and that is reflected in the end price you pay.
End-to-end service, cutting-edge facilities.
From our expert product design and performance testing facility in Scotland, our specialist team work with clients on research and development, design, colour and texture selection, and prototyping. With meticulous attention to detail, we specialise in creating bespoke products that elevate your brand.
Design: Our specialist, full-service, in-house team understands the practicalities of designing with leather better than anyone, and we know what works for production at high volume. We work closely with our clients and taking even the most ambitious design requests, we use our expertise to find the right balance. Then, we refine, refine, refine, to develop that final design.
Testing: At Muirhead, we ‘pre-stress’ test prototypes by exposing them to extreme temperatures and humidity that simulate years of real-world service. Continuous benchmarking against competitor products ensures that we deliver on our performance promises. And we can certify whole-seat constructions to the most demanding of international standards.
Production: Our dedicated, state-of-the-art, fast-turnaround, cut-and-sew facility holds AS9100 rev D approval for high-volume finished leather seat cover production. Our smart cutting technology uses AI to maximise the yield of every individual leather hide and our skilled team hand-sew every single seat cover we make. Costs are reduced, waste is minimised, and the carbon footprint is lowered. Our bespoke lamination technology delivers increased comfort and rigidity while reducing weight and simplifying fixing for shorter cover change times.
“We look at how best to engineer the leather to make it work at high volume; changing the amount of leather, reducing the sewing time, testing different foam specifications, different laminations, and so on.” - Charlotte Clayton, Cabin Engineering Manager
Two service streams: Line-fit and Retro-fit.
For our core Line-fit service, we work directly with seat manufacturers (OEMs) to supply brand new seats for fleets of new aircraft or trains, under direction from the airline or rail operator.
With Retro-fit, we collaborate with the airline or train company to refresh their existing stock, incorporating a whole new interior scheme, design upgrade or colour change. We also offer a first-time fitting service – a step-by-step tutorial for in-house engineers, detailing how to handle, manipulate, clean and fit the leather.
No matter if you come to us with a new or existing fleet, you benefit from Muirhead’s simplified supply chain, leather expertise, and design experience, ensuring a flawless end result that meets your exact requirements.
Proven capabilities, remarkable results.
Muirhead Seat Covers are already flying on major global airlines and client feedback has been universally and overwhelmingly positive. Our service has been praised by clients for solving their long-standing challenges, following years of frustration with other suppliers.
By combining decades of leather expertise with modern, cutting-edge design and production processes, we have been able to deliver a simplified, streamlined and sustainable seating supply model, unlike anything else in the market.
“Where we have finished projects, the response has been absolutely outstanding. They’ve all said the product is fantastic, we’ve fixed their problems, the cabins look incredible.” - Martin Longden, Head of Cabin Engineering
To find out more about the Muirhead Seat Cover Service, and to try our seat covers for yourself, pay us a visit at the Aircraft Interiors Expo 2025 (AIX), Booth 6E95.